Vernetzte Fertigung
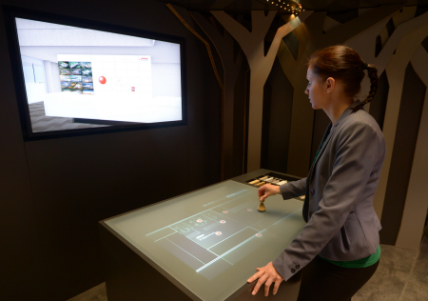
In vier Stunden von der rohen Spanplatte bis zum fertigen Möbelstück in Losgröße 1 – das ist heutzutage kein Problem mehr. Dabei kann aus einer Breite von vielen Millionen möglichen Produktvarianten jeder individuelle Kundenwunsch erfüllt werden. Foto: Messe Hannover/Ligna
In vier Stunden von der rohen Spanplatte bis zum fertigen Möbelstück in Losgröße 1 – das ist heutzutage kein Problem mehr. Dabei kann aus einer Breite von vielen Millionen möglichen Produktvarianten jeder individuelle Kundenwunsch erfüllt werden. Befürchteten viele Betriebe durch den unaufhaltbaren Trend zur Individualisierung anfangs noch steigende Kosten, so haben inzwischen perfekte wirtschaftliche Lösungen die Bedenken zerstreut. Moderne Fließfertigung vereint hohe Kapazität mit maximaler Flexibilität. Das Werkstück durchläuft prozesssicher und schnell eine beliebig lange Produktionskette von der Planung, der Arbeitsvorbereitung über den Zuschnitt, die Kantenanleimmaschine und die CNC-Bearbeitung bis hin zur Montage- und Verpackstation. Dank modularem Aufbau sind die Anlagen in der Lage, dem Wachstum des Betriebes zu folgen.
Immer im Fluss
Miteinander kompatible Softwaremodule, die auf die Schnittstellen der CNC-Maschinen abgestimmt sind, sorgen in diesem System für kontinuierlichen Teile- und Informationsfluss. Je nach Bedarf ist jede gewünschte Maschinenkonfiguration möglich. Ein Gesamtsystem von 100 CNC-Achsen und mehr ist keine Seltenheit. Module gibt es für nahezu jeden Prozess. Platten können in kürzester Zeit an jeden beliebigen Lagerort transportiert oder zur Bearbeitung auf einem angeschlossenen CNC-Center bereitgestellt werden. Andere Module sorgen nach dem Abarbeiten der Schnittliste durch die Säge für ein automatisiertes Restemanagement, das bis zur vollautomatischen Resterückführung ins Lager reicht. Abstapel-Programme sagen dem Bediener oder dem Roboter, wo das Werkstück abgelegt werden muss. Dazu kommt ein großes Angebot an Optimier-Software, das von der Fertigungsplanung über den Zuschnitt bis hin zum Maschinen-Management reicht. Das Resultat sind weniger Materialverbrauch und höhere Ausbeute.
Vollautomatischer Prozess
Ein wichtiger Bestandteil des vernetzten Prozesses ist die Teilelogistik entlang der Prozesskette. Automatische Säge-Lager-Kombinationen übernehmen heute die mannlose Vorkommissionierung, gewährleisten automatische Bestandskontrolle und -überwachung und sorgen für eine optimale Disposition. Die Software wählt dabei auftragsbezogen aus einem Bestand von mehreren Hundert verschiedenen Platten aus. Ebenso kann sie die Effizienz der Lagerhaltung analysieren und Vorschläge zur Verbesserung unterbreiten.
Bei der Werkstückverfolgung haben sich von der Möbelindustrie bis hin zum Fensterbauer Auto-ID-Lösungen durchgesetzt. Dabei werden auf dem Werkstück mittels Etikettendrucker Informationen aufgebracht, die vom Scanner im Laufe des weiteren Produktionsprozesses identifiziert und von den Maschinen umgesetzt werden. Informationen wie die Reihenfolge der benötigten Teile oder die Art der vorgesehenen Bearbeitung können so ohne viel Aufwand übermittelt werden. Mehr Informationstiefe bietet die RFID-Technologie. RFID funktioniert mit Barcode-Label, aber auch mit im Werkstück implementierten Transpondern, die sich über die gesamte Prozesskette verfolgen lassen und alle Prozessparameter der Anlage verwalten. Die Daten werden automatisiert im ERP-System miteinander verknüpft. In der innovativen Oberflächentechnik steuert auf diese Weise zum Beispiel die Lackiermaschine automatisch den Farbwechsel an, Trockentemperatur und Vorschub regeln sich von selbst, Rezepturen werden automatisch abgerufen.
Auch die Werkzeughersteller sind aktiv an der Entwicklung beteiligt. Sie steuern innovative Tool-Management-Systeme bei, die den Arbeitsprozess erleichtern. Unter anderem ermöglichen sie eine schnelle, zuverlässige Verbrauchs- und Kostenanalyse der eingesetzten Werkzeuge inklusive voraussichtlicher Standzeit.
Vom Studio in die Fabrik
Schon gibt es erste Steuerungsarchitekturen, die als integrierte Lernsysteme mit digitalem Produktgedächtnis kundenspezifische Ideen in Realität umsetzen. In nicht allzu langer Zeit, meinen Insider, werden Planer und Architekten ihre Entwürfe direkt an die Möbelfabrik senden, die sie dann in Losgröße 1 automatisch produziert. Wo heute noch der Bediener entscheidet, was mit dem Werkstück passieren soll, werden bald autark agierende Maschinen diese Aufgabe selbstständig und datengetrieben übernehmen und so eine transparente, lückenlose und prozesssichere Vernetzung garantieren.
Der aktuelle Stand der Technik bei der vernetzten Fertigung lässt sich auf der Messe Ligna erleben: vom 11. bis 15. Mai in Hannover.
www.ligna.de