Öfen im Sekundentakt
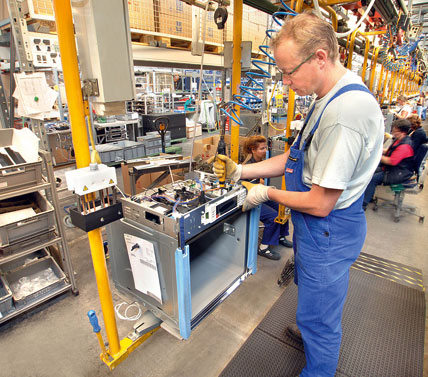
Ein Mitarbeiter montiert die E-Box, die quasi die Schaltzentrale des Backofens ist. Die Backmuffel ist hier bereits isoliert und verkleidet.
Mit den Küchen-Einbaugeräten der Generation 5000 will Miele im obereren und mittleren Preissegment weltweit weiter wachsen. In die Forschung und Entwicklung für diese neuen Einbaugeräte hat das Unternehmen insgesamt rund 51 Mio. Euro investiert, nicht mitgerechnet sind dabei die Kosten für Marketing und Vertrieb weltweit. Die neuen Geräte in Miele-Qualität, getestet auf 20 Jahre Lebensdauer, lassen sich aufgrund ihrer einheitlichen Gestaltung optisch harmonisch miteinander kombinieren. Ganz gleich, ob Backofen, Dampfgarer, Kaffeevollautomat oder Speisenwärmer über- oder nebeneinander eingebaut werden, das Miele-Design wirkt wie aus einem Guss. Experten haben deshalb die klaren Linien und Strukturen ebenso gelobt wie die unkomplizierte Bedienung und die vielfältigen Automatikprogramme der neuen Miele-Einbaugeräte. Zur Markteinführung wurden bereits vier Miele-Geräte, darunter auch Modelle der Generation 5000, mit dem „iF gold award“, einem der international renommiertesten Design-Preise, ausgezeichnet. Zwölf Geräte bekamen den „iF product design award 2008“ des International Forum Design in Hannover. Die Jury lobte die klare Formensprache und das authentische Produktdesign von Miele. Benutzer verstehen die Funktionen auf Anhieb und können die Geräte sofort bedienen.
10 Millionen für Oelde
Mit einem Investitionsvolumen von mehr als zehn Millionen Euro für Produktionsanlagen hat Miele das Werk in Oelde zu einer der modernsten Produktionsstätten für Herde und Backöfen ausgebaut. Diese Investitionen flossen in neue Produktionsanlagen, auf denen jetzt eine neue Generation von Herden und Backöfen – Geräte der Generation 5000 – hergestellt wird. Im Miele-Verbund ist das Oelder Werk Kompetenzzentrum für Herde und Backöfen. Hier produziert das ostwestfälische Unternehmen jährlich über 260.000 Geräte für den weltweiten Markt.
Eine neue Fertigungslinie für Garräume macht mit sieben Millionen Euro die größte Einzelinvestition aus. Auf dieser Anlage werden Garräume – im Fachjargon auch Backmuffeln genannt – mit einem Volumen von 43 und 66 Litern produziert. In der Küche kann sich der Kunde so für einen 60 Zentimeter breiten und 60 Zentimeter hohen Backofen mit einem 66 Liter fassenden Garraum und fünf Einschubebenen entscheiden. Oder er wählt einen Kompakt-Backofen, der bei ebenfalls 60 Zentimeter Breite nur 45 Zentimeter Höhe für 43 Liter Garraum benötigt. So bleibt in der Höhe noch 15 Zentimeter Platz für eine Wärmeschublade. Aus den vielfältigen Ausstattungsvarianten kann sich der Kunde ein – zu seinen persönlichen Anforderungen und Bedürfnissen passendes – Modell aussuchen.
###newpage###
Mit schnellen Umrüstzeiten für Werkzeuge ist die gesamte Anlage flexibel ausgelegt. Die ersten Schritte auf dem Weg zum fertigen Garraum sind das Prägen und Stanzen der Bleche. Die vorgeformten Bleche werden danach mit Rückwand und Deckenblech verschweißt. Das geschieht vollautomatisch und so präzise, dass von den Schweißnähten später nichts mehr zu sehen sein wird. Alle 30 Sekunden verlässt eine Backmuffel die Anlage, die von einem Mitarbeiter bedient wird. Als sogenannte Volumengeräte machen die auf dieser Fertigungslinie produzierten Backöfen und Kompakt-Backöfen den Großteil aller in Oelde hergestellten Herde und Backöfen aus. Auf zwei weiteren Fertigungsstraßen entstehen Garräume für den neuen 90 cm breiten Backofen, für ein 70 cm breites Gerät sowie für die Master-Chef-Modelle, die mit einem Volumen von über 100 Litern auf den nordamerikanischen Markt zugeschnitten sind. Insgesamt sieben verschiedene Garraumgrößen bilden die Basis für über 700 Modell- und Ausstattungsvarianten – ein außergewöhnlich breites Spektrum, das maßgeschneiderte Lösungen für Kundenbedürfnisse in aller Welt bietet.
Tauchbad im Starkstrom
Ein komplexer Vorgang ist das Emaillieren der Garräume. Die entfetteten und gespülten Backmuffeln werden nach dem von Miele entwickelten ETE-Verfahren (elektrophoretische Tauchemaillierung) behandelt. Garräume und Backbleche werden dazu in ein unter Starkstrom gesetztes Bad getaucht. Das Email haftet in diesem Bad besonders gut an den glatten Blechen und bildet eine gleichmäßige Oberfläche, die nach dem folgenden Brennvorgang extrem robust ist. Rund 3,5 Mio. Euro hat Miele in eine neue Emaillieranlage investiert, mit der die Kapazität des Werkes gesteigert werden konnte. Das ETE-Verfahren ist übrigens für Miele patentiert. Bei der PerfectClean-Veredelung erhalten Garräume, aber auch Backbleche und anderes Zubehör, nach der Emaillierung eine einzigartige Oberflächenveredelung – PerfectClean. Lebensmittel können auf dieser Oberfläche kaum anbrennen, was den Reinigungsaufwand sehr erleichtert.
Das aufwendige Herstellungsverfahren für Garräume und Zubehörteile im Backofen trägt zu einer langen Lebensdauer bei, ist aber im Gesamtprozess der Entstehung eines Backofens quasi nur die Vorstufe. In der Montage kommen wesentliche Komponenten dazu: Heizkörper, Isoliermaterial, Backofentür und die sogenannte E-Box samt angeschlossener Bedieneinheit. Stromversorgung und Elektronik sind in die E-Box integriert, die damit quasi die Funktion der Schaltzentrale für den Backofen hat.
www.miele.de